
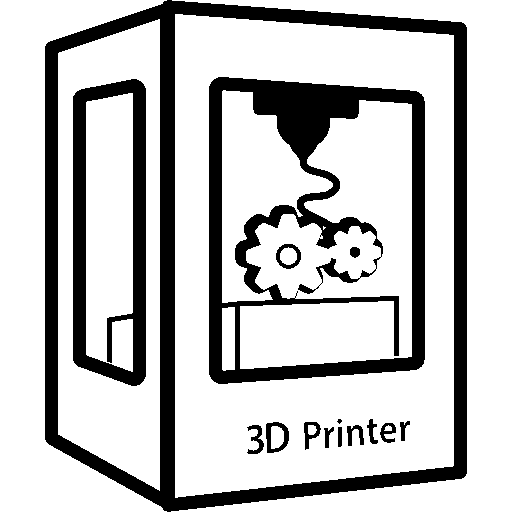
the granules are blue when dry and turn purple/red when they no longer absorbs humidity.
Don’t buy those. Orange gel is the “new” blue.
The reason why the blue gel was phased out decade(s) ago is the CoCl2. Along all of the hazards are H350i and H360F (cancer and reproduction [aka. your plan to have kids might not turn out that great]).
While orange gel doesn’t have as good of a color change it is significantly lower risk and shall be used.
China. That’s where you can still get the Cobalt indicator and subsequently on Amazon, Aliexpress or ebay.
The upside is the fantastic color change, which is why some still prefer it and why it is probably still being made.
In Europe there is an alternative blue indicator that is cobalt-free, but it is more of a blue to brown/very dark red colour change, so not great either especially after a few drying cycles.