
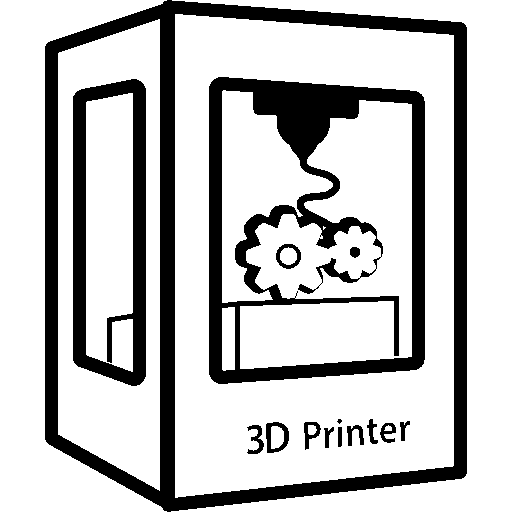
6·
2 days agoIts not about torque only.
If build up correct, the nozzle flange does not touch the aluminium heater block. There must be a gap, can be a tiny gap.
You dont want to screw the nozzle against the block, but you want to screw the nozzle backside face (around the filament bore) against the heatbreak end face. This is the place where you close the oozing hole, the threads are not tight against liquid plastic.
@Prunebutt
There is no seal like an o-ring.
It is bare metal to metal surface contact.
If there is a gap between nozzle backside end and heatbreak because the outer hexagonal part of the nozzle hit the heater block first (before the nozzle get tight at the heatbreak), it will leak through the treads and ooze out on the top.
If you can rotate the heaterblock after heating up the nozzle, then there is proof of the inside gap.
On a new hotend i disassemble it before mount it into the printer, screw in the nozzle in first and then turn it back half a turn.
Then screw the heatbreak in until it reaches the nozzle. Install it to the printer, heat to max used temperature, and tighten the nozzle again.
The heater block has bigger thermal expansion, so it tends to get loose by heating up.
If done correct you will never have problems like this, if the mating surfaces are even and not damaged.